A. Carbon tool steel
T8A and T10A carbon steel tool steels are widely used in molds and have the advantages of good processing performance and low price. However, the hardenability and red hardness are quite different, and the heat treatment deformation and bearing capacity are low.
B. Low alloy tool steel
Low-alloy tool steel is based on carbon tool steel with an appropriate amount of alloying elements. Compared with carbon tool steel, it reduces the quenching deformation and cracking tendency of steel, and improves the hardenability and wear resistance of steel. Low-alloy steel used for mold manufacturing includes CrWMn, 9Mn2V, 7CrSiMnMoV (code ch-1), 6CrNiSiMnMoV (code GD), etc.
C. High carbon and high chromium tool steel
Commonly used high carbon and high chromium tool steels include Cr12, Cr12MoV, Cr12Mo1V1 (code D2), SKD11, etc., which have good hardenability, hardenability and wear resistance. The heat treatment deformation is very small. It is a high wear resistance and micro-deformation die steel, and its bearing capacity is second only to high-speed steel. However, due to the serious segregation of carbides, multiple upsetting (shaft upsetting, radial drawing) is required to improve the performance and reduce the unevenness of carbides.
High carbon medium chromium tool steel
High-carbon medium-chromium tool steels for molds include Cr4W2MoV, Cr6WV, Cr5MoV, etc., with low chromium content, less eutectic carbides, uniform carbide distribution, small heat treatment deformation, good hardenability, and good dimensional stability. Compared with high-carbon and high-chromium steel with severe carbide segregation, its performance has been improved.
E. High-speed steel
High-speed steel has the highest hardness, wear resistance and compressive strength among die steels. Commonly used in molds, W18Cr4V (code 8-4-1) with less tungsten content, W6Mo5 Cr4V2 (code 6-5-4-2, American brand M2) with code 6-5-4-2, developed to improve toughness Carbon vanadium reduction high-speed steel 6W6Mo5 Cr4V (code 6W6 or low carbon M2). HSS also needs to be modified to improve its carbide distribution.
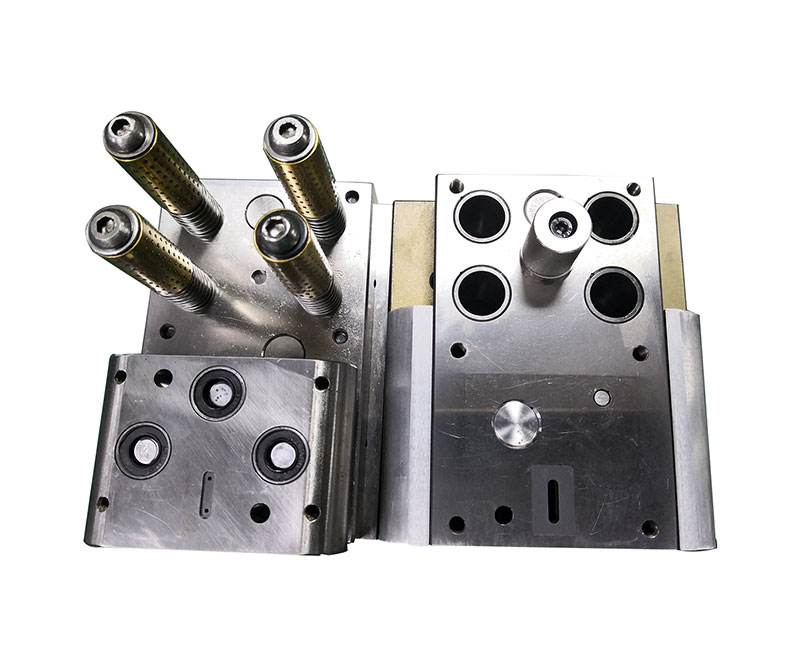
F. Base steel
In order to improve the performance of high-speed steel, a small amount of other elements are added to the basic composition, and the carbon content is appropriately increased or decreased. This kind of steel is collectively referred to as base steel. They not only have the characteristics of high-speed steel, have certain wear resistance and hardness, but also have better fatigue strength and toughness than high-speed steel. Cold die steel has high strength and toughness, and the material cost is lower than high-speed steel. The commonly used base steels in molds are 6Cr4W3Mo2VNb (code 65Nb), 7Cr7Mo2V2Si (code LD), 5Cr4Mo3SiMnVAL (code 012AL) and so on.
G. Cemented carbide and steel bonded cemented carbide
The hardness and wear resistance of cemented carbide are higher than any other type of die steel, but the bending strength and toughness are poor. The cemented carbide used in the mold is tungsten-cobalt, which requires less impact and higher wear resistance. For high-impact molds, cemented carbide with high cobalt content can be used.
Steel-bonded cemented carbide is made of titanium carbide or tungsten carbide as the hard phase, adding iron powder and a small amount of alloying element powder (such as chromium, molybdenum, tungsten, vanadium, etc.) as a binder, and sintered by powder metallurgy. The base of steel-bonded cemented carbide is steel, which can be processed, welded, forged and heat treated. Steel cemented carbide contains a large amount of carbides. Although its hardness and wear resistance are lower than that of cemented carbide, it is still higher than other steel grades. After quenching and tempering, the hardness can reach 68 ~ 73HRC.
h. New materials
The material used in the die is cold-worked die steel, which is the most widely used type of die steel and has a large application volume. The main performance requirements are strength, toughness and wear resistance. The development trend of cold work die steel is based on the performance of high alloy steel D2 (equivalent to Chinese Cr12MoV), which is divided into two branches: one is to reduce the carbon content and the number of alloying elements, and to improve the uniformity of the steel carbide distribution , Highlight the toughness of the mold. Such as 8CrMo2V2Si from Vanadium Alloy Steel Company in the United States and DC53 (Cr8Mo2SiV) from Datong Special Steel Company in Japan. In order to improve the wear resistance of high speed, automation and mass production, another powder high speed steel was developed. Such as German 320CrVMo13 and so on.