Sheet Metal Services
Sheet Metal Fabrication Services
Mould-in-China employs sheet metal technology to bend, punch, and cut standard gauge metals for both rapid prototypes and low to high-volume production runs. What set us apart from other conventional sheet metal shops is our incredible capacity and proficiency in sheet metal manufacturing of end-use and durable metal parts or components coupled with broad material selections and finishes matching your needs.
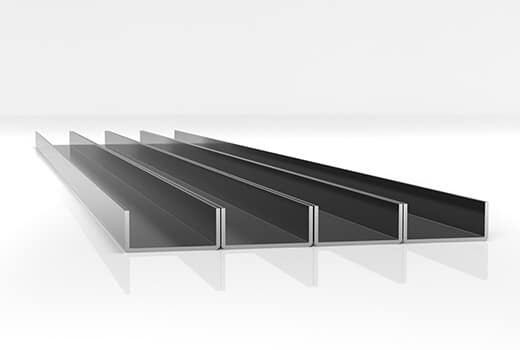
What is Sheet Metal Fabrication
Sheet metal fabrication is a subtractive manufacturing process involving forming parts from thin metal sheets by cutting, bending, folding, punching, and assembling. Sheet metal can be cut, bent, or stretched into almost any shape, usually by cutting and burning the metal. Sheet metal parts are usually highly precise and durable, making them particularly preferred by engineers to use for end-use applications such as enclosures, brackets, and chassis.
If you rightly have demands on custom sheet metal fabrication or outsourcing manufacturing of your sheet metal parts to a reliable supplier in China, Mould-in-China may be your premier choice. You have access to get in touch with our team of knowledgeable engineers and machinists to get a fast and cost-effective solution for any kind of parts.
How Does Sheet Metal Fabrication Work
The sheet metal fabrication processes start with removing materials from thin sheet metal stock placed on a flat bed following programmed part patterns to form desired shapes by cutting tools. This operation can be finished with a variety of subtractive machining processes. A sheet metal punch, shear, laser, waterjet, or plasma can generate additional features such as internal holes and edge features according to the part geometry.
The second stage is material deformation. After being cut, the parts reach the press brake where they are formed into the final geometries with the forming process such as bending.
The last stage is to assemble pieces of sheet metal or fit them together with other components that are not made from sheet metal into a complete product. In many cases, surface finishing operations are needed to enhance mechanical properties.
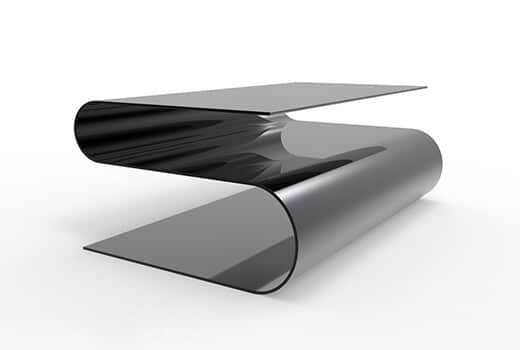
Available Sheet Metal Fabrication Processes
Thin sheets of metal can be manipulated through different processes as they are more malleable than thick workpieces. Moreover, sheet metal fabrication offers competitive prices for low-volume prototypes and saves costs for high-volume production runs. Mould-in-China offers high precision cutting, bending, punching, and welding, as well as assembly services.
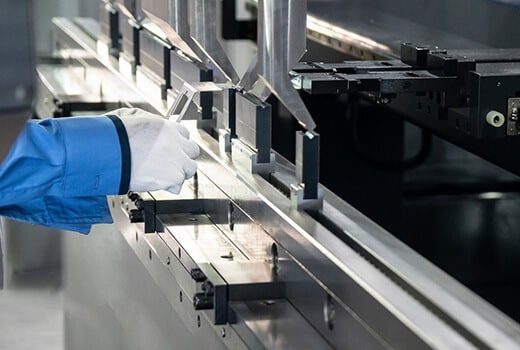
Sheet metal bending is a manufacturing process that uses dies to generate a V- shape, U-shape, or channel shape along a straight axis in ductile materials. It is applied to shape stainless steel, steel, and aluminum parts, and rapid prototyping of custom sheet metal after the cutting process.
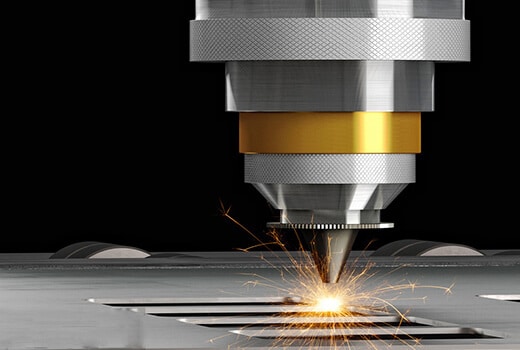
This manufacturing process uses a high-density light beam to cut a thin sheet metal in which CNC is useful in control of either the laser beam or the workpiece. Intense lasers can cut through sheet metals 0.5mm to 20mm thick to prototyping sheets for abundance parts.
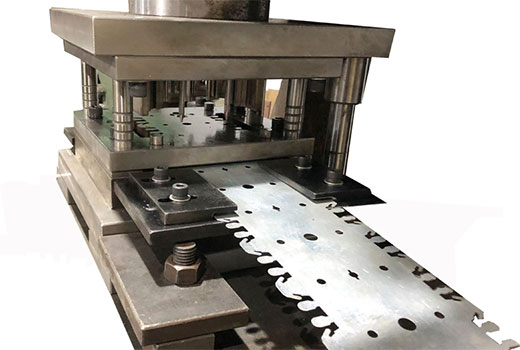
Stamping is a manufacturing process that involves the use of punches and dies to imprint shapes and designs onto metal sheets. This process applies intense pressure to the metal, forcing it to conform to the desired shape or pattern into various parts and components.
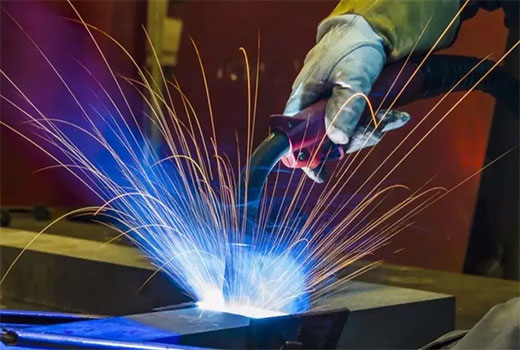
Welding refers to the uniting or fusing of pieces by using heat and/or compression so that the pieces form a continuum. The source of heat in welding is usually an arc flame produced by the electricity of the welding power source. Arc-based welding is called arc welding.