Vacuum Casting: The Process and Benefits
Vacuum casting is a manufacturing process that involves pouring a liquid material into a mold cavity under vacuum pressure. The process is commonly used to create small to medium-sized parts with intricate details, such as prototypes, jewelry, and toys.
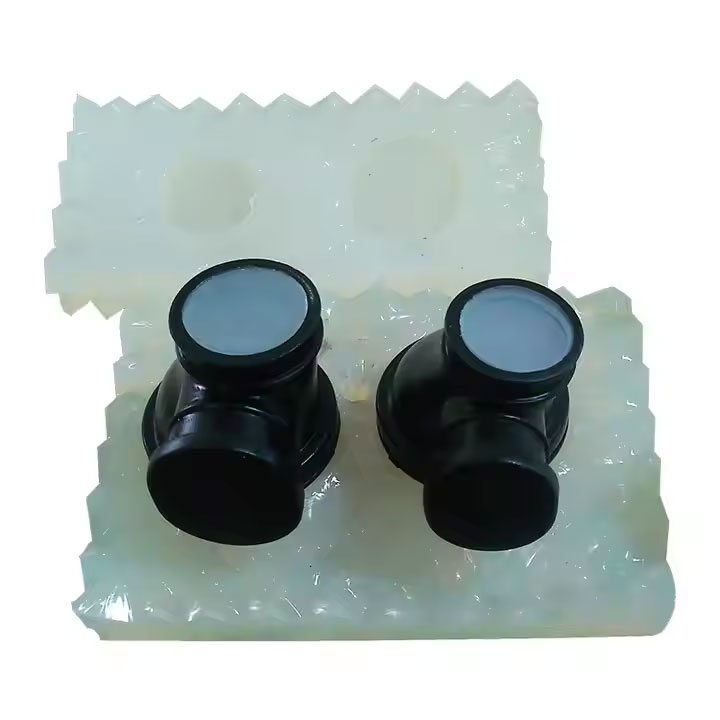
The process begins by creating a master pattern using 3D printing or CNC machining. A silicone mold is then created from the master pattern. The mold is placed in a vacuum chamber, and the liquid material is poured into the mold. The vacuum pressure removes any air bubbles from the mold, ensuring that the final product is free of defects.
One of the main benefits of vacuum casting is its ability to produce high-quality parts with excellent surface finishes. The process is also cost-effective, as it allows for the creation of multiple parts from a single mold. Additionally, vacuum casting can be used with a wide range of materials, including plastics, resins, and metals.
Vacuum casting is a popular choice for prototyping and small-scale production runs. It allows for the creation of complex parts with a high degree of accuracy and repeatability. The process is also flexible, allowing for modifications to be made to the mold as needed.
In conclusion, vacuum casting is a valuable manufacturing process that offers numerous benefits. Whether you’re creating a prototype or producing small parts for a product, vacuum casting can help you achieve your goals with ease and efficiency.